QUALITY CONTROL AND EXPERIMENTS IN CONCRETE
- Safa Turna
- Aug 2, 2023
- 2 min read
Concrete is the most widely used building material in the construction industry. The quality of concrete is very important for the safety and performance of structures. For this reason, quality control and testing of concrete should be carried out carefully during the concrete production and application stages.
Quality control and testing of concrete is carried out in three main stages:
- Quality control of concrete before casting
- Quality control during concrete casting
- Quality control after concrete has been poured or after a structural element has been constructed
The quality control of concrete before casting aims to determine the suitability of the components of concrete (cement, aggregate, water, admixtures) and the mixing proportions. Some of the tests to be performed at this stage are as follows:
- Cement tests: The chemical composition, physical properties, strength and compatibility of cement are tested.
- Aggregate tests: Parameters such as size distribution, shape, surface properties, density, water absorption capacity, content of harmful substances are measured.
- Water tests: Chemical properties of water such as pH, hardness, salinity, chloride and sulphate content are analyzed.
- Additives tests: The compatibility of admixtures with cement and aggregate and their effects on concrete (increase or decrease in consistency, change in setting time, strength development, etc.) are analyzed.
Quality control during the pouring of concrete aims to ensure that the transportation, placement and compaction of concrete are carried out correctly. Some of the tests to be performed at this stage are as follows:
- Fresh concrete tests: These are performed to determine the consistency (slump test), air content (compressed air test), temperature (thermometer measurement) and density (unit volume weight test) of fresh concrete.
- Sampling tests: Cube or cylinder-shaped samples of fresh concrete are taken and sent to the laboratory. These samples are then used for hardened concrete tests.
Quality control after the concrete has been poured or after a building element has been constructed aims to test the strength and durability of the concrete. Here are some of the tests that need to be carried out at this stage:
- Hardened concrete tests: Mechanical properties of laboratory cured specimens such as compressive strength (cube or cylinder crushing test), flexural strength (beam crushing test), modulus of elasticity (measured by dynamic or static methods) are determined.
- Non-destructive tests: These are methods used to measure the strength or quality of concrete in a structure without destroying it. Examples include ultrasonic wave velocity test, coring test, Schmidt hammer test, carbonation depth test, chloride content test, etc.
Quality control and testing of concrete are scientific and technical studies necessary to determine and improve the quality of concrete. These studies ensure that appropriate standards and regulations are complied with during the design, production and application stages of concrete. Thus, it is possible to use concrete as a safe, robust and durable building material.
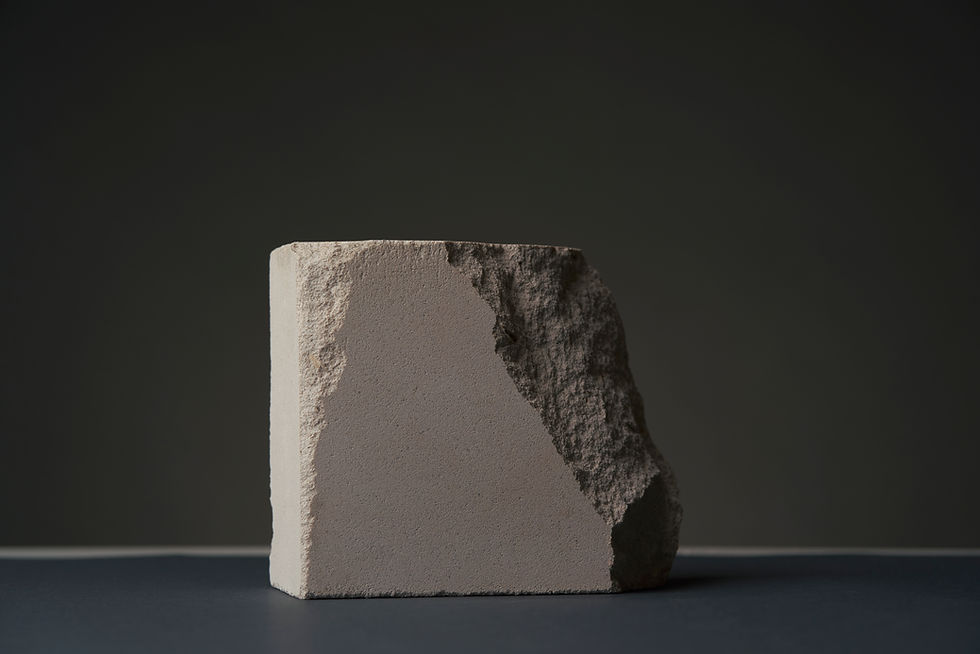
Comments